WHAT IS RISO
Risograph printing was established by Noboru Hayama in Tokyo in 1946, starting with Hayama mixing inks at his kitchen sink. The word “riso” means “ideal” in Japanese, a reminder for Japan’s people to “not lose their ideals” and future as a nation after World War II, according to Hayama. Risograph was born out of the mimeograph printing process, the first Riso printer-duplicator being invented in 1986 by Hayama’s Riso Kagaku Corporation.
The Risograph machine brings together several printing processes previously done manually, a blend of mimeograph, Gocco, and the Gestetner system. Original artwork is scanned through the machine, after which a thermal plate burns the image onto a “master sheet,” similar to a printing screen. The master is then wrapped around a drum, which pushes ink through the voids in the master as the drum rotates at high speed, duplicating the image onto the paper.
Riso printers use a soy-based ink and does not require heat to fix the image onto the paper, unlike a photocopier or laser printer, resulting in an output that can be treated like any offset-printed material. Riso ink is also low in harsh pollutants normally found in petroleum based ink, making Risograph a more planet and budget friendly printing method.
WHAT CAN RISO DO?
Riso printing creates rich and vibrant colors, with a distinct texture similar to offset printed work or graphic novels. A wide spectrum of color combinations are possible, as Riso machines use halftones to reproduce the image. These halftone dots combined with the translucent nature of Riso ink allows for interesting color overlays and a unique look to each print. Risograph’s unpredictable imperfections lead to each print having personality, distancing the work from the polished and impersonal nature of digital print.
WHAT CAN RISO NOT DO?
As stated, Risograph printing is not for artists looking for a perfect duplication, and is limited to the number of colors available. Because each color of ink uses a dedicated drum, Riso is also incapable of reproducing full color images simultaneously. Some mis-registrations may occur during the printing process, so we do not recommend Riso for multi-layered projects that require a high level of tight registration. Please see below for more information on Riso’s important factors to consider.
HALFTONES
All Riso prints have some level of grain, part of the appeal of the method. The Risograph will perform halftone translations without any assistance, but we also recommend printing your original with a halftone screen in the event that you are printing photographs or high-detail work. If you have any questions about this process,
please feel free to reach out, and we can happily make a recommendation!
HAPPY ACCIDENTS:
UNEVEN COVERAGE, SMUDGING, AND TRANSFERPlease note that areas in your artwork including large fields of color may have uneven coverage. This is to be expected, though we do strive to ensure that your prints will be as evenly coated as possible.
Because Riso ink is non-archival, similar to newspaper ink, ink may smudge if pressure is applied. While the likelihood of smudging decreases as the print ages, it is always possible when handling your prints with natural skin oils. It’s best to handle prints carefully, using gloves or washing your hands frequently if necessary. Some smudges can be removed with a rubber eraser.
If your prints use heavy ink coverage, there is the chance of ink transferring or rubbing onto the back of the prints when stacked.
MISREGISTRATION
While we will do our best to ensure that your project’s layers will be correctly registered, each layer is printed separately, which means that some misregistration is likely. There may be up to 5mm of shift between prints due to the movement of the machine, press shift, and feed rotation.
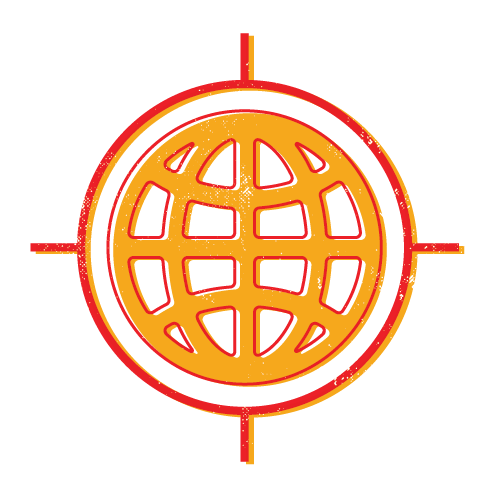
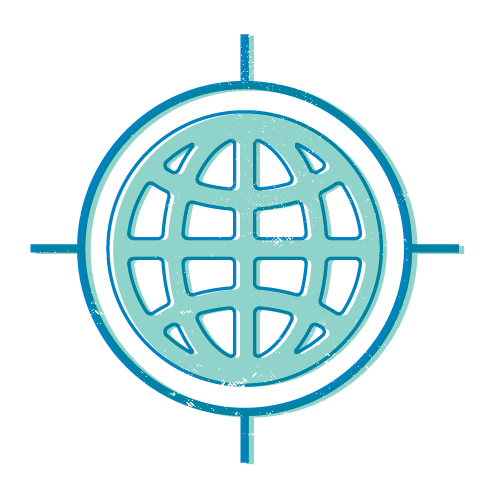
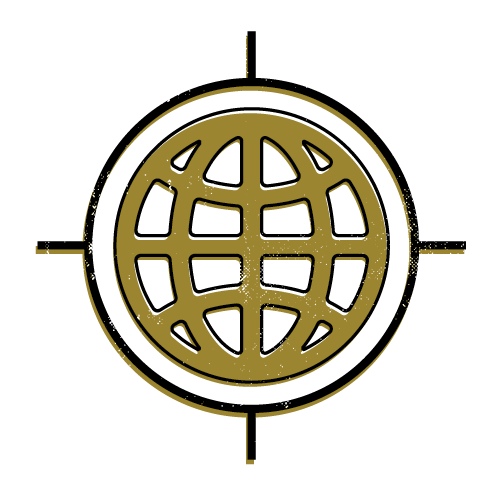
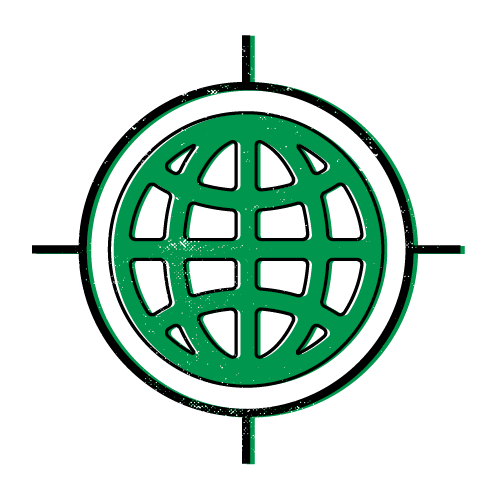
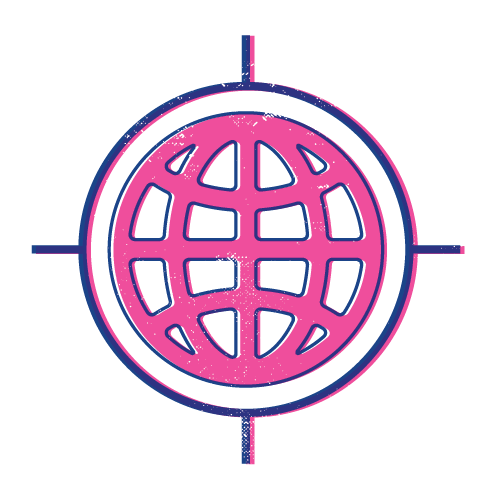
ROLLER MARKS
Paper is fed through the Riso with a rubber wheel, applying pressure to the page. With fresh ink, this may leave a “roller mark” at the bottom center of the print. These are most noticeable when artwork includes dense ink coverage near the paper feed edge, and with specific ink colors. Roller marks can often be removed with a rubber eraser, when appearing in blank or lightly covered areas of the paper. If roller marks are a concern for your project, please reach out to us with the intended artwork, and we can gladly consult with you if this should be an issue!
